Mechanical Engineering Infrastructure
Farnham SAI Installation
Farnham STW – Thames Water had identified a Spend to Save initiative to replace the existing lime dosing plant at Farnham STW.
As a result, Gel Engineering worked with Thames Water to replace the existing lime dosing plant and with a new (S)mart (A)ir (I)njection system significantly reducing the number of points of failure, maintenance requirement and consumption per KW/h .
GEL acted as Principle Contractor and Principal Designer responsible to produce all relevant designs, RA/MS, CPP, H&S File and Programme of Works to fulfil requirements under CDM 2015.
GEL worked closely with our sister company LOS Electrical to provide a full turn key solution.
Management, supervision & monitoring of the scheme throughout the duration of the works.
Works consisted of the removal of existing multistage screw conveyor network, conditioning screws, slewing belt system and safely emptying and disposing of unspent lime and lime storage silo.
Mechanical Installation of new Smart Air Injection system.
Sludge Mains
Scope of Works
Replacement of the existing 230m twin Sludge Main running along wall and steelwork gantry over the road.
Installation of new sludge pipe, jointing, welding 460m of 315 SDR17 pipework
Installation of 8 No Steel Bellows Expansion joints
Installation of 230m of Armco barriers
Drain down existing pipes, remove sludge, and dispose of pipes offsite for recycling
Installation of 5mm Aluminium pipe cladding
Challenges
One of the biggest challenges to overcome for GEL on the project was the design, pipe expansion ‘behaviour’ and installation of a new ‘sludge main’ whilst one line of existing sludge main remained ‘online’. This was completed without delay to the project and without any downtime to the Sewage Treatment Works, which happened to be the biggest n Europe.
Our Responsibility
Working closely with The Client, GEL proposed changes to the existing sludge main to enhance quality and sustainability. The new sludge main was constructed using pipe made from recycled plastic with old pipework sent for recycling; the solution was, therefore, environmentally friendly as well as cost effective and sustainable.
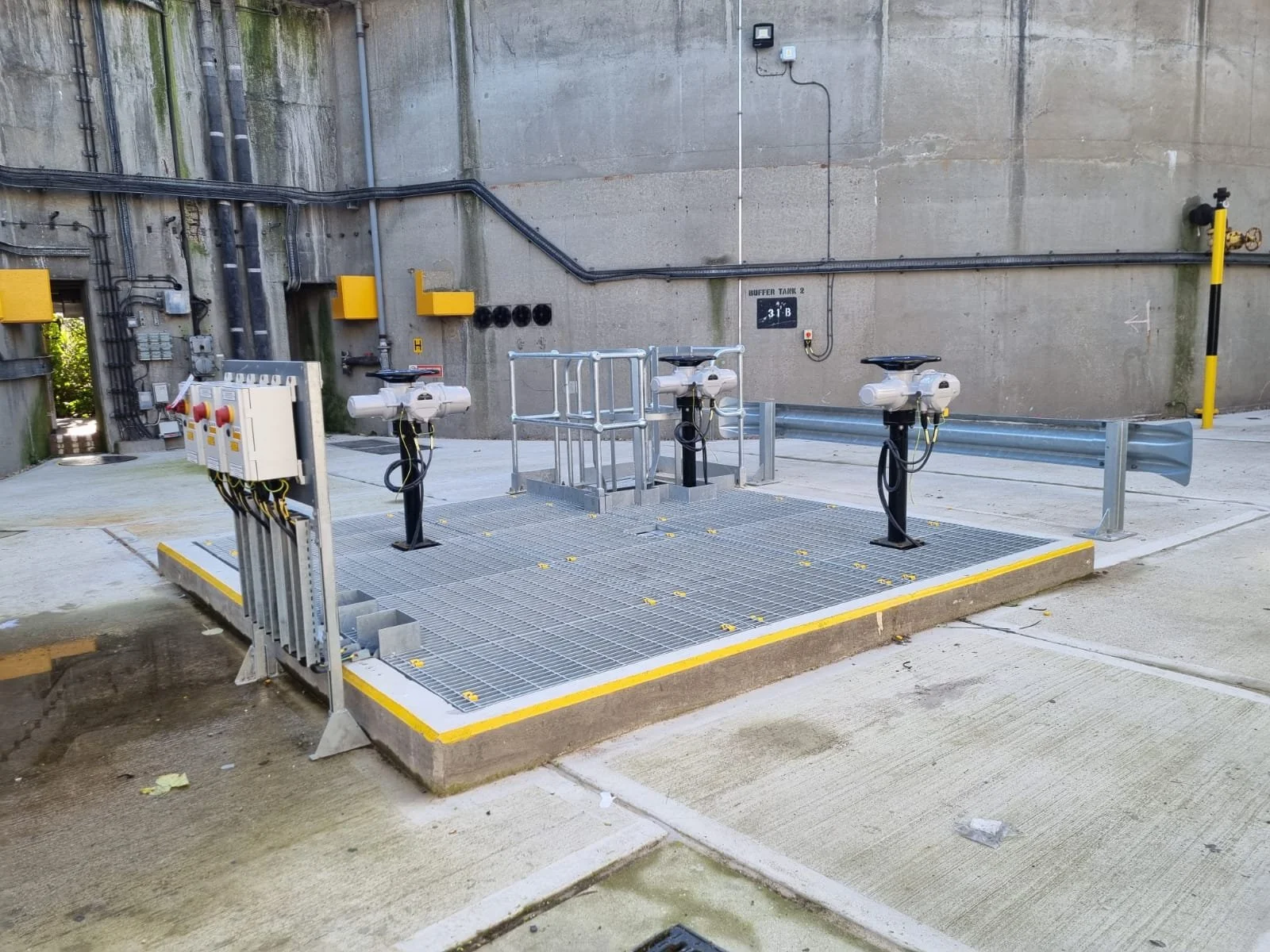
Valves and Chamber Improvements
-
Chamber A (Before)
The scope of works was to replace the existing tank outlet valves within the outlet chambers and install a new downstream isolation knife gate valve.
-
Chamber A (After)
The Client also required the concrete roof slab to be replaced with a grated steel platform and suitable lighting. Gel Engineering devised an innovative solution to assist the Client in the complex task of draining the buffer tanks to enable the works.
-
Chamber B (Before)
As the project progressed the Client’s needs evolved to include concrete aprons to the surrounding area and additional minor works.
-
Chamber B (After)
We always take a comprehensive and holistic view to our Client’s needs. GEL believe continuous engagement and clear communication are vital to ensure a project’s success. In any project, a client’s needs are always developing, and we like to ensure that these requirements are promptly met with a suitable and often innovative solution.